復合材料零部件可以轉載在金屬切削機床上進行加工,也可以采用與切削金屬零件類似的刀具。然而,一旦刀具切削刃切入復合材料工件,就能揭示出與金屬切削的本質區別——二者的材料去除機理完全不一樣。
金屬切削加工的材料去除機理是塑性變形。工件材料比刀具材料軟,在刀具切削刃上會形成切屑流。而在切削加工復合材料時并不會產生真正意義上的切屑。工件材料并不是被剪切去除,切削刃的作用是切碎堅硬的碳纖維。在此過程中,切削刃要承受劇烈的磨蝕,這可能會導致其快速磨損。
在金屬切削加工中,刀具的幾何形狀決定其切削性能,刀具材料決定其使用壽命。復合材料的切削加工也同樣如此。在加工復合材料時,刀具材料也會成為其切削性能的一個決定因素。復合材料可能會造成刀具快速磨損,從而使刀具幾何形狀迅速改變——除非切削刃材料能夠抵御復合材料的磨蝕,足以保持其幾何形狀和鋒利性。鉆削加工復合材料時,一種常見的現象就是,可能加工出的前兩個孔都具有良好的鉆出孔口質量,但很快就會在第三個孔出現分層、開裂或其他孔口缺陷,這是因為刀具的磨損導致其幾何形狀再也無法保持干凈整齊的切削。
關鍵詞:金剛石刀具,復合材料,切削加工
引言
波音787是世界上第一種主要由碳纖維復合材料制成的大型商用客機:復合材料占到這種飛機結構重量的50%和飛機體積的大約80%。與之相比,波音777型客機所用復合材料的重量僅占11%。波音公司正在實現一個重大承諾:用復合材料取代金屬材料。航空公司從中獲得的經濟效益可以解釋這樣做的原因。如何切削加工復合材料對于一架飛機而言,初始購機成本在其最終總成本中并不占大頭。飛機的維修成本和燃油成本加起來占到其運行總成本的大部分。而使用復合材料可以顯著降低這兩方面的成本。與金屬材料相比,航空復合材料本身具有更好的抗疲勞性和耐腐蝕性,從而在波音787的整個服役期間能節省高達3,000-4,000萬美元的維修費用。復合材料結構還提供了更大的強度/重量比,有利于節省燃油成本。據估計,與飛行里程相同的波音767(一種較小的客機)相比,一架波音787每年節省的燃油費用可達500萬美元。如何切削加工復合材料通過采用復合材料而在維修和燃油成本上節省的費用,以及在其他方面節省的各種成本,加起來差不多已經接近這架飛機的價格。也就是說,可以這樣理解:如果這架飛機是用復合材料制成的,那你幾乎就是免費獲得了這架飛機。
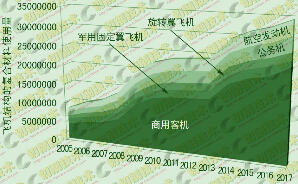
直升機后部的水平尾翼通常用鋁合金制成。這種鋁合金部件有時會被阿帕奇直升機發射導彈時產生的噴射流所損壞,這種噴射流會以大約每秒2,000英尺的速度向后高速沖擊水平尾翼。而復合材料部件能更好地抵御這種沖擊。此外,這種新的復合材料尾翼重量更輕,制造成本也更低,可謂“一舉幾得”。
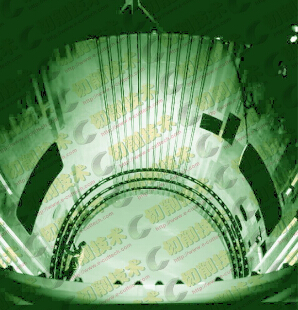
復合材料零件是一種近凈成形工件。為了加工出要求的零件形狀,需要將這種形狀復制在專門定制的刀具上。與鋁合金航空結構件相比,復合材料零件需要進行的切削加工要少得多。但話又說回來,復合材料零件需要進行的切削加工確實極具挑戰性。復合材料的定義方式與金屬材料不同。“復合材料”是將兩種或多種材料組合到一起,以獲得比單獨采用其中任何一種材料更優異的性能。在復合材料中,一種材料是基體,另外一種(或多種)材料起補強作用。碳纖維增強塑料(CFRP)是飛機零部件常用的主要復合材料,由塑料基體和起補強作用的碳纖維構成。嘗試加工這種復合材料的生產車間面臨著雙重挑戰:塑料基體可能會因為切削溫度過高而融化;而碳纖維可能會因為破碎(而不是平穩剪切)而變得難以切削。同時,CFRP結構件是由各層材料疊合而成,在切削加工時可能容易出現開裂或分層現象。
最后一個挑戰在于:當準備對復合材料結構件進行切削加工時,它已經成為一個價值不菲的工件,如果加工報廢,可能會蒙受巨大的經濟損失。
因此,隨著越來越多的復合材料零件進入市場,更多的加工車間將面臨這樣一種現實:與金屬零件相比,復合材料工件的加工量更小,但加工的成本更高、難度更大、價值更昂貴、影響更嚴重。
并不只有波音公司在推動復合材料發展。實際上,幾乎所有的飛機制造商都越來越多地用復合材料來替代某些金屬零件和組件。現在,直升機也大量使用復合材料。事實上,各種高附加值產品制造商正越來越多地尋求采用這種或那種形式的復合材料,以利用其高強度、高剛性、耐久性、耐腐蝕性、耐磨損性和重量輕等優勢。有人預計,在未來10年中,用于風力發電機的碳纖維復合材料可能會比用于所有飛機的CFRP更多。同時,金屬基復合材料正被應用于高性能汽車零部件(如剎車盤等)。此外,由于復合材料能夠透過X射線,因此可能還會在醫療行業發現許多新的用途。
然而,在討論此類材料時,上述措辭——“這種或那種形式的復合材料”——給出了一個重要提示,即復合材料并不是一類具有統一標準的材料。
例如,碳纖維復合材料(CFRP)是一種聚合物增強塑料,其中包括許多不同的品種。同樣,金屬基復合材料和陶瓷基復合材料的規格品種也五花八門。實際上,“復合材料”一詞所指的范圍比“金屬材料”范圍更廣。
美國俄亥俄州的合同制造商General Tool公司的數控編程和刀具主管Earl Wilkerson曾經面對各種不同復合材料的加工挑戰。他認為,復合材料可以是“人們希望將其組合在一起的任何兩種材料。”
當你面對一種從未加工過的復合材料時,如何知道正確的加工方法呢?你很可能對此毫無頭緒。這是復合材料加工的現實狀況。在這一點上,General Tool公司可以算是復合材料加工專家。該公司很早就開始加工采用復合材料的噴氣發動機,有15年以上加工航空復合材料的豐富經驗。即便如此,每一種新的復合材料零件對其加工車間仍然是一種新的挑戰。
事實上,每一種新的碳纖維復合材料(CFRP)零件都各不相同。“CFRP”本身的范圍很廣。General Tool公司在其第一種CFRP零件的加工獲得成功后,在加工第二種CFRP零件時又麻煩不斷,直到它發現,應該降低加工所用的切削參數,并增大加工某些零件特征所需的毛坯余量,因為第二種CFRP的特性和成分與第一種CFRP截然不同——這是復合材料加工的典型特點。Wilkerson指出,“為了確定合適的刀具、切削速度和進給率,你不能只是去查一本切削手冊,在其中尋找有關‘復合材料’的內容。你甚至都無法找到加工CFRP的內容。對這些材料的加工還缺乏足夠明確的定義或一致性。”
不過,從事復合材料加工的生產車間還是總結出了一些有用的經驗——這些經驗使它們在加工某一類復合材料時能持續獲得成功,雖然復合材料的種類還在不斷增加和變化。
1 復合材料加工機理
切削加工復合材料可能看起來與切削金屬材料大同小異,但實際上,二者的加工機理大相徑庭。
復合材料(如CFRP)零件可以裝夾在金屬切削機床上進行加工,甚至也可以采用與切削金屬零件類似的刀具(雖然這種可能性較小)。然而,一旦刀具切削刃切入復合材料工件,就能揭示出與金屬切削的本質區別——二者的材料去除機制完全不同。
金屬切削加工的材料去除機制是塑性變形。工件材料比刀具材料軟,在刀具切削刃上會形成切屑流。而在切削加工復合材料時(這里主要考慮CFRP),并不會產生真正意義上的切屑。相反,用“粉碎”來描述材料去除機理可能更為貼切。工件材料并不是被剪切去除,切削刃的作用是切碎堅硬的碳纖維。在此過程中,切削刃要承受劇烈的磨蝕,這可能會導致其快速磨損。
在金屬切削加工中,刀具幾何形狀決定了其切削性能,刀具材料決定了其使用壽命。復合材料的切削加工也同樣如此。不過,在加工復合材料時,刀具材料也會成為其切削性能的一個決定因素。復合材料可能會造成刀具快速磨損,從而使刀具幾何形狀也迅速改變——除非切削刃材料能夠抵御復合材料的磨蝕,足以保持其幾何形狀和鋒利性。鉆削加工復合材料時,一種常見的現象就是,可能加工出的前兩個孔都具有良好的鉆出孔口質量,但很快就會在第三個孔出現分層、開裂或其他孔口缺陷,這只是因為刀具的磨損導致其幾何形狀再也無法保持干凈整齊的切削。
在某種程度上,加工復合材料實際上是將加工流程前后顛倒,因為加工車間的注意力轉移到了加工流程的不同部分。加工金屬材料航空零件可能需要大功率機床,但只需使用普通刀具,且用簡單的夾具就能確保加工的安全性。與此相反,銑削和鉆削復合材料通常是在功率小得多的輕型機床上進行,但可能需要采用高端刀具,并要使用專門定制的夾具,以便在整個加工過程中緊密支撐工件,防止其剛性薄壁產生振動和破損。
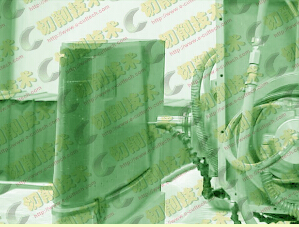
(1)刀具材料
硬質合金刀具可以用于加工復合材料,但由于壽命較短,在加工過程中往往需要頻繁換刀。
金剛石刀具可能具有更長的使用壽命。加工CFRP時,可選擇的金剛石工具包括電鍍金剛石磨粒的修磨棒、CVD金剛石涂層刀具或整體式PCD刀片。
為加工復合材料而專門開發的一種不同尋常的刀具是“整體燒結”金剛石刀具,該刀具是將金剛石材料填充在硬質合金刀柄上專門設計和加工出的狹槽中,直接燒結成型。
(2)刀具幾何形狀
至少在一個方面,復合材料的“粉碎”去除機理與金屬材料的“變形”去除機理有相似之處:正如在金屬切削中一樣,切削能量也會轉化為熱量。
CFRP的散熱特別困難,因為加工時不會產生能帶走熱量的切屑,加之復合材料的導熱性很差。由此造成的熱量積聚使基體材料面臨融化或以其他方式受損的危險。冷卻液可能也于事無補,因為有些復合材料零件的加工不允許使用冷卻液。因此,只能通過合理選用刀具和走刀路徑來抑制切削熱。
一般來說,尖銳的刀具切削角是減少切削熱的關鍵要素之一。銑削和鉆孔復合材料的刀具通常都采用大正前角,以最大限度地減少發熱量,實現快速、鋒利、整潔的切削。這些刀具也具有較大的后角,足以防止刀具切削刃在走刀時與工件摩擦發熱。


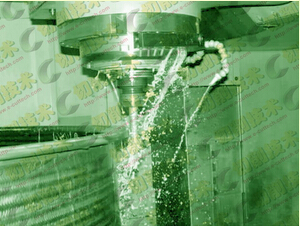
復合材料航空零部件的輪廓形狀一般需要用五軸聯動機床加工。有些以前加工金屬零部件的車間可能會使用自己原有的五軸機床。不過,加工復合材料(至少是加工CFRP)時,通常并不需要加工金屬材料時那樣大的機床功率和扭矩。事實上,在一些通常無法勝任金屬零件加工的輕型CNC鏤銑床上,往往能夠有效地加工CFRP和其他復合材料。
2 復合材料的銑削加工
General Tool公司正在見證復合材料加工需求的不斷增長。該公司擁有240名員工和大約40臺CNC數控金屬切削機床。迄今為止,該公司的加工車間已設法將其復合材料加工限制在其中3臺機床上。之所以要對加工復合材料的機床加以限制,部分是因為切削復合材料(主要是CFRP)時產生的粉塵很難管理。不過,Wilkerson先生表示,復合材料的加工需求正變得越來越大,他認為3臺機床將很難長期滿足這種加工需求。
在該加工車間,復合材料工件的銑削加工相當普遍(圖6)。那些尺寸較大、外壁較厚的復合材料零部件(尤其是噴氣發動機的外殼)需要進行大量的側銑和面銑加工。孔加工通常也會涉及到銑削,因為該車間為了滿足苛刻的質量要求,需要首先鉆削出直徑較小的孔,然后再將其銑削加工到最終直徑尺寸。
CFRP的銑削加工通常采用電鍍金剛石刀具。典型的粗銑刀用粒度為25目的金剛石顆粒制成,可能會采用9.5mm的徑向切深。典型的精銑刀用粒度為100-180目的金剛石顆粒制成,其徑向切深可能僅為0.25mm。
Wilkerson表示,該車間曾經確信,為了更好發揮金剛石刀具的切削性能,就需要提高切削速度,而其最大規格復合材料加工機床的主軸轉速僅為5,000r/min。因此,為了將較低的主軸轉速轉換為較高的表面切削速度,就需要采用大直徑的電鍍金剛石刀具。但隨著時間的推移,該車間發現,電鍍金剛石刀具即使在較低的轉速下,也能獲得不錯的切削性能。事實上,低速加工對抑制切削熱更有利。
現在,General Tool公司用電鍍金剛石刀具銑削加工復合材料的經驗和設備已轉化為一筆可觀的技術資產,使其在承接復合材料加工任務時處于有利地位。即便是某種特定類型的CFRP銑削加工,可能也與該車間以前曾遇到過的加工任務有所不同,但該車間知道如何選用合適的刀具和切削參數,至少可以在有效加工一種新的零件時有一個良好的開端。此外,該車間可能已有現成的合適刀具,這是很大的優勢——一個重要復合材料加工項目所用的金剛石刀具價格可能超過1萬美元,而且從頭開始確認和訂購這些刀具可能需要長達12周的交貨時間。
復合材料的銑削加工可能代價不菲,但與復合材料的鉆削加工相比,其加工難度可能并不算大。
3 復合材料的鉆削加工
鉆削往往是復合材料零件加工的真正挑戰。在金屬零件上鉆孔時,只需去除工件材料并對孔進行清理即可。與此不同的是,在多層結構的復合材料上鉆孔時,鉆頭可能會推擠各層材料,并在出口一側造成不可接受的分層剝離、開裂等缺陷。
Wilkerson認為,用標準的金屬切削鉆頭鉆削復合材料工件,就像鉆削沒有支撐的膠合板一樣,會將復合材料工件的鉆出孔口撕裂。因此,鉆削復合材料通常需要使用量身定制的專用鉆頭。
由于復合材料孔加工的技術要求和潛在挑戰各不相同,因此其鉆削刀具產品也多種多樣。用于CFRP孔加工的刀具設計具有以下一些特點:
(1)采用中心直刃鉆尖設計,鉆尖位于刀具中心,使周邊切削刃可以像飛刀那樣進行切削。
(2)鉆鉸刀具有各自獨立的切削刃,可用一把刀具同時完成鉆削和鉸削加工。
(3)采用磨制的八面體鉆尖,這種結構設計可使鉆尖的副切削角具有自定位功能,并能使刀具磨損分散到更多分離的切削刃上,從而延長刀具壽命。
(4)采用雙刃帶結構的定心階梯鉆頭可以提高復合疊層材料的鉆削精度。
刀具供應商肯納金屬公司也開發了各種復合材料加工刀具。該公司專門研究CFRP鉆削的研發工程師Karthik Sampath提供了設計更高效復 合材料孔加工刀具的一些共同要點:
(1)為了減小會導致分層剝離的切削力,采用正的刀具幾何形狀至關重要。
(2)螺旋角、后角和齒隙前角都遵循以下規律:隨著角度增大,鉆孔質量趨于改善。
(3)減小鉆尖角有利于提高鉆出孔口的質量。不過,鉆尖角過小可能會降低刀具的切削刃強度。對于加工CFRP的鉆頭,最佳折衷方案似乎是采用90°鉆尖角。與之相比,鉆削金屬材料時,較典型的鉆尖角為135°(即加工復合材料的鉆頭“更尖”)。
Sampath表示,加工CFRP時,金剛石涂層刀具通常會比未涂層刀具的使用壽命提高10倍以上。他通過實驗,對不同厚度(5-16μm)的金剛石涂層進行了評估,結果表明,涂層厚度為12μm的金剛石涂層刀具具有最佳的壽命/價格比。
鉆削復合材料時,對加工質量的關注通常集中在鉆出孔口。但Sampath指出,有時也需要注意有問題的鉆入孔口缺陷。當鉆頭鉆入時,可能會使復合材料最上面的一層扭曲變形。出現這一問題通常表明鉆削進給率太小。通過增大進給率,往往可以減少入口缺陷——雖然這樣做可能會使出口缺陷增大。應選用能兼顧入口和出口兩側質量的最佳進給率。
General Tool公司的Wilkerson表示,他經常選用國際硬質合金公司(International Carbide Corporation)提供的WonderDrill鉆頭來加工一些特定的復合材料零件。該鉆頭利用正的鉤形刃口將復合材料中的增強纖維“拉入”切削刃,從而加工出表面光潔的孔。這種外形簡潔的刀具去掉了所有多余的刀槽,以提高其強度和剛度(圖10)。然而,即便使用這種刀具,General Tool公司通常也不會依賴鉆削加工來達到孔的最終尺寸,因為這樣做使缺陷增多的風險極大。為了確保孔的質量,該公司通常是先鉆削一個比最終直徑尺寸小0.50-0.75mm的預孔,然后再用電鍍金剛石精銑刀以圓弧插補方式銑孔至最終尺寸。
4 用“水刀”加工復合材料
美國賓州的Hydrojet公司有兩臺福祿公司(Flow International Corporation)生產的磨料水射流(俗稱“水刀”)加工機床。該公司工程師Jack Seibert表示,作為一個小型加工車間,他們通過高效加工復合材料零件,找到了自己的利基市場,而其他規模較大的飛機零部件制造商很難以一種成本效益好的方式進行這種加工。很多復合材料零件都需要用磨料水刀進行修邊。不過,并非所有零部件都適合水刀切割。因此,該車間最終又增加了一部分銑床,現在它有三臺哈斯公司(Haas Automation)生產的加工中心和一臺X軸行程達4m的大型CNC鏤銑床。
Seibert指出,應采用水刀加工還是常規切削加工,主要取決于零件的幾何尺寸和形狀。大型零件可以首選水刀加工,因為用水刀切割工件時,不需要使用專門的夾具。但是,用水刀加工一些特殊廓形工件會出現一個問題,即用噴射水流切割預定的加工面時,可能會意外切割到工件上其他一些不應切割的表面。如果某個零件的廓形使其本身幾乎能平行對折,可能就不適合采用水刀切割,而必須在加工中心上切削加工。
其他一些因素也可能會影響加工方式的選擇。加工精度就是一個重要因素。加工中心的精度更高,因此更適合加工公差要求嚴苛的復合材料零件。另一個考慮因素是工件材料。水刀能夠有效加工各種不同類型的復合材料。例如,凱芙拉纖維是一種極難銑削加工的復合材料,常常令加工車間頭痛不已,而利用水刀則可以輕松地加工凱芙拉零件。