晶片制備工藝中金剛石線是耗費較高的一個因素,研究并分析影響線鋸壽命的機能就至關重要。本論文討論了線鋸表征方法并研究了金剛石線的磨損情況。研究結果表明:金剛石線和加工材料間的相互作用引起的切割線磨損(CWW)以及金剛石線本身的作用而引起的非切割線磨損(NCWW)是金剛石線磨損的兩種主要形式。在新型實驗裝置上,NCWW被降低至最小,顯著改善了金剛石線的切割性能。
關鍵詞:金剛石線,磨損,切割,機械優(yōu)化
引言:
光伏設備用碳化硅晶片的制備工藝近年來正經(jīng)歷著一場技術革新,以金剛石線加工為代表,也即固結磨粒鋸切(FAS)技術正替代漿加工和自由磨粒鋸切(LAS)技術。這種技術革新不僅影響著碳化硅晶片的多線鋸加工工藝,還改變著光伏產業(yè)鏈中其他碳化硅切割工藝,如晶錠修整等。FAS技術中耗費較高的就是金剛石線鋸損耗。金剛石線的最大使用時間也即線壽命主要受線磨損影響。本論文主要研究金剛石線的磨損對制造設備的影響。
論文分為以下部分:首先介紹金剛石線在整個耗費中的占比;然后分析金剛石線磨損的實驗方法,主要是制造設備方面線損的特征和原因,最后介紹了經(jīng)設備優(yōu)化的高性能金剛石線。
金剛石線在整個耗費中的占比
圖一為金剛石線設備耗費計算。(a)為晶片制造總費用(從結晶到質檢);(b)為生產線加工耗費(非碳化硅);(c)晶片耗費分布比例。
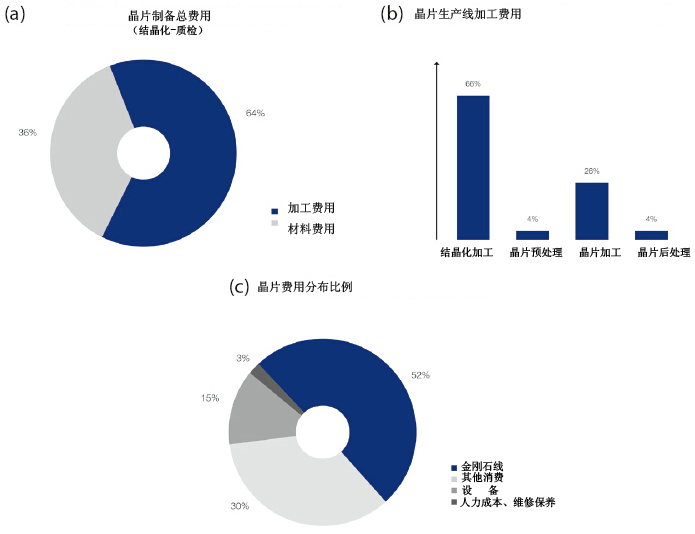
圖一:成本計算
然后,根據(jù)一條完整的晶片生產線加工步驟將加工費用細分為幾個部分(圖一b)。為避免繁瑣,修整、磨削和上膠等程序都歸為預晶片處理;清理、測量和打包歸為后晶片處理;圖表中可以看出除了結晶化工藝處理是高能耗外,晶塊切割成片是最大的耗費之一,占整個加工耗費的四分之一。
晶片處理費用中,金剛石線占據(jù)將近一半的費用比例(圖一c)。本實驗中金剛石線占整個費用的比例為9%。根據(jù)pvinsights.com的數(shù)據(jù)統(tǒng)計,2013年8英尺單晶碳化硅晶片的平均價格為1.2美元。根據(jù)晶片制造商的利潤,金剛石線耗費占每片晶片的8%-9%。由此可以看出降低金剛石線耗費對于晶片費用的影響。如果一條線鋸的線耗費縮減10%,那么一臺年產量350000片的機器就可以節(jié)省開支35000美元。
金剛石線性能
晶片加工中,金剛石線消耗可以通過切割一塊晶片所用的線長(m/片)或單位長度的線長切割出的晶片面積(cm2/m)來量化。第二個定義有兩點好處:不依賴晶片面積且易轉化為其他切割工藝參數(shù),如晶錠修整等。因此,本論文中主要討論金剛石線性能,而不討論線消耗。
為最大化金剛石線性能,延長線的操作時間(線壽命)就十分必要;在實際生產過程中,就是要重復多次使用同一根線來完成切割。向前進級幾百米后,調換線的進給方向;在向后進給幾百米后,再次調換進給方向。
線性能設置的過高,會出現(xiàn)切割精度下降和線斷裂現(xiàn)象。最適宜的線性能基本保持在切割表面的規(guī)格和線成本之間。
線性能增大引起的切割精度下降的機能尚未研究清楚,但作者認為金剛石線的磨損是最主要的限制因素。因此,為了定義最適宜線性能的工藝,有必要建立對線磨損進行表征的分析方法。
金剛石線分析方法
一種最直接的金剛石線分析方法是利用測微規(guī)測量線直徑,這是一種無損測量方法,測量結束后線還可以繼續(xù)用來切割。圖四和圖六為該方法測得的數(shù)據(jù)結果。
對于晶片加工,線直徑可以由晶片厚度獲得;為此,需要知道線的外徑和晶片表面的距離。假設該距離保持常量,那么根據(jù)晶片厚度的變化就可以求得線的外徑,如圖三和五所示。
利用光學顯微鏡對金剛石線進行觀察。在實際操作中,為獲取線狀態(tài)的高分辨率圖,通常采用SEM進行觀察法。研究線磨損的測量技術如圖二、四、六所示。
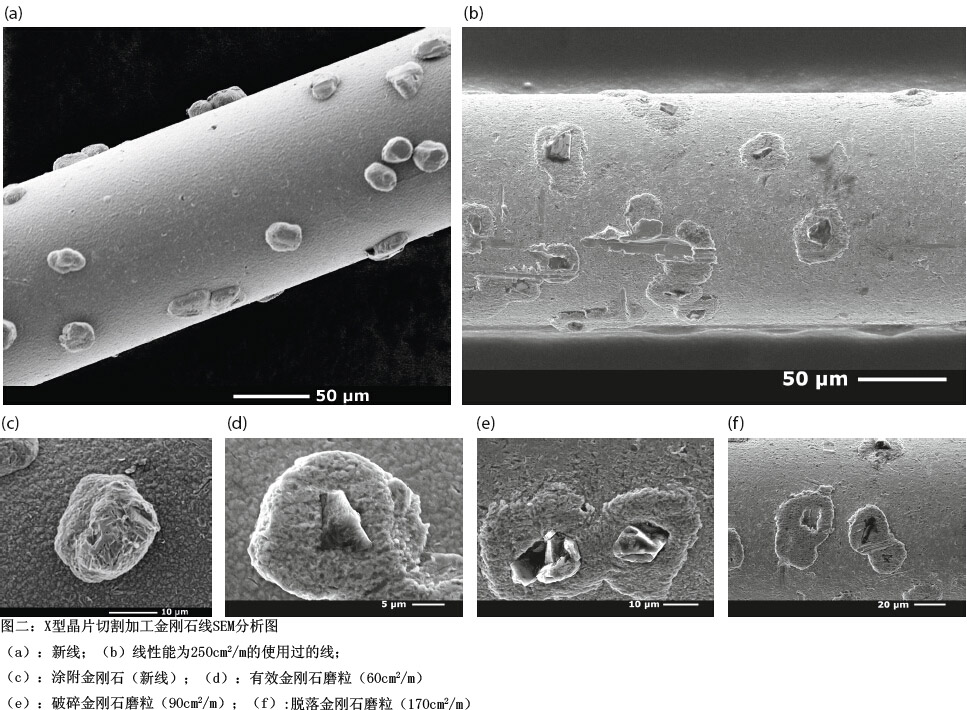

為研究金剛石線的磨損特征,實驗對X型商用金剛石線進行SEM分析,結果如圖二所示。圖二(a)中,利用一個嶄新的金剛石線采用上述進給方向對四個碳化硅晶片進行切割加工,線性能為250cm2/m。圖中最后一排為持續(xù)切割階段的金剛石線特寫。
隨著線性能的增加,線外徑變小。這種變小和使用過的金剛石線特征相關聯(lián)(圖二b,d,e,f),如變形、金剛石突起的脫落和金剛石破碎;同時切削力也增大。這些現(xiàn)象都和金剛石線的磨損有關。
金剛石線磨損的原因
以上金剛石線磨損描述留下了一個最基本也是最重要的問題:什么機能引起了線磨。文獻中除了提及線磨對晶片制造成本的重要性外,并無涉及引起線磨的機能。此外,還有一個問題就是跟金剛石線的機械接觸在何處發(fā)生。切割過程本身會使金剛石線和被切割材料發(fā)生接觸;其他接觸還有:線和導絲輥上面的涂附材料接觸;線和滑輪、纏線軸發(fā)生的接觸;以及纏線時線本身相互間的接觸。切割過程中線和被切割材料發(fā)生的磨損稱之為切割線磨損(CWW),其他情況引起的磨損稱之為非切割線磨損(NCWW)。很顯然,為降低線的耗費,在切割性能確定的參數(shù)條件下,CWW應該保持最小,NCWW盡可能要避免。
下一步就是研究造成NCWW的機械接觸類型都有哪些,以及如何量化這些類型。由于同一根金剛石線上可能會同時出現(xiàn)CWW和NCWW,所以這一問題解決起來比較困難。
論文的其他部分主要討論在纏線和卸線的過程中引線卷軸上發(fā)生的金剛石線本身的機械接觸。為研究這種接觸是否影響切削過程,實驗對晶片厚度做了分析,如圖三所示。
利用傳統(tǒng)的多線鋸和Hennecke晶片監(jiān)測系統(tǒng)用Y型金剛石線對125mm(6’’)的單晶碳化硅晶片進行切割;沿著25mm寬的條帶平均分布測厚點。在1022塊測試晶片中,有3塊晶片厚度超過180μm,將其剔除在實驗分析之外。
第2、3、4個25mm條帶的平均值分別用向下的三角形、方形和向上的三角形表示,如圖3所示。
對比圖三中曲線間的不同可以看出:切割過程中(從向下的三角標識到向上的三角標識)晶片平均厚度增大。這說明金剛石線的外徑由于線磨損而變小。金剛石線的橫截面SEM圖可以看出,與金剛石線相互垂直的方向上有典型的刮痕,如圖2b所示。
通過氣割還可以測量到線外徑的減少,氣割是線鋸上材料負載為零的晶片切割加工。實驗證明:通過對金剛石線操作管理系統(tǒng)的精微調整,可以降低線外徑的磨損。總之,在每100周期的纏線和卸線循環(huán)中有最小為0.4μm的 外徑減小量可以觀測到。
鏡片加工過程中線磨損的降低
從以上線磨損機制可以看出,對晶片加工設備的優(yōu)化可以實現(xiàn)成本節(jié)省。事實上,傳統(tǒng)晶片加工設備的金剛石線操作系統(tǒng)都是為自由磨粒鋸切(LAS)技術而研發(fā)的;該技術中金剛石線自身的接觸是無害無損的,因為線本身并不包含任何切割磨粒(如金剛石),也就不會磨損相互接觸的其他金剛石線,進而不會影響切割性能。而固結磨粒鋸(FAS)切技術中金剛石線自身的接觸可以引起額外的磨損。因此,從LAS到FAS技術的轉變就需要對金剛石線操作系統(tǒng)進行設備上的優(yōu)化處理。
Meyer Burger研發(fā)了一種金剛石線操作管理系統(tǒng)的多線鋸設備原型,能夠在金剛石線纏線和卸線中最大化的減小線接觸并多次重復使用,如圖4、5所示。

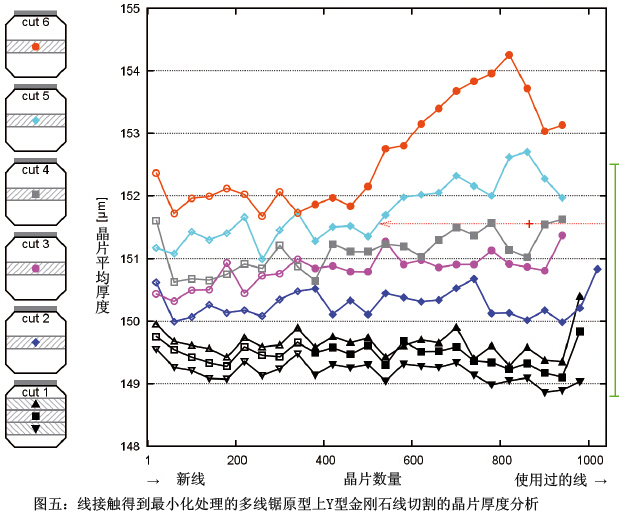
采用X型金剛石線對硅晶片進行切割加工,線性能為420cm2/m;另選線性能為500cm2/m的Y型金剛石線進行切割加工。觀察發(fā)現(xiàn),兩種類型的金剛石線在纏線和卸線過程中都沒有機械磨損帶來的垂直刮痕。還可以觀察到有效金剛石磨粒,如圖4b所示。對比兩種類型的金剛石線外直徑發(fā)現(xiàn),線磨損是線性能的一個函數(shù),如圖4a所示。
以上實驗結果說明線接觸經(jīng)過最小化處理的晶片加工設備可以實現(xiàn)高性能的金剛石線切割加工。如圖四所說明,成本節(jié)省取決于金剛石線的類型。
結論:
晶片制備工藝正經(jīng)歷有自由磨粒鋸切技術向固結磨粒鋸切技術的轉變,其中金剛石線是最主要的消耗因素。本論文對纏線和卸線過程中線接觸對金剛石線的磨損情況進行了研究分析;通過對現(xiàn)有線操作管理系統(tǒng)的精微調整,NCWW可以得到一定程度的減小。而要想進一步減少線磨損,就需要對金剛石線管理系統(tǒng)進行創(chuàng)新改造。(編譯:中國超硬材料網(wǎng))